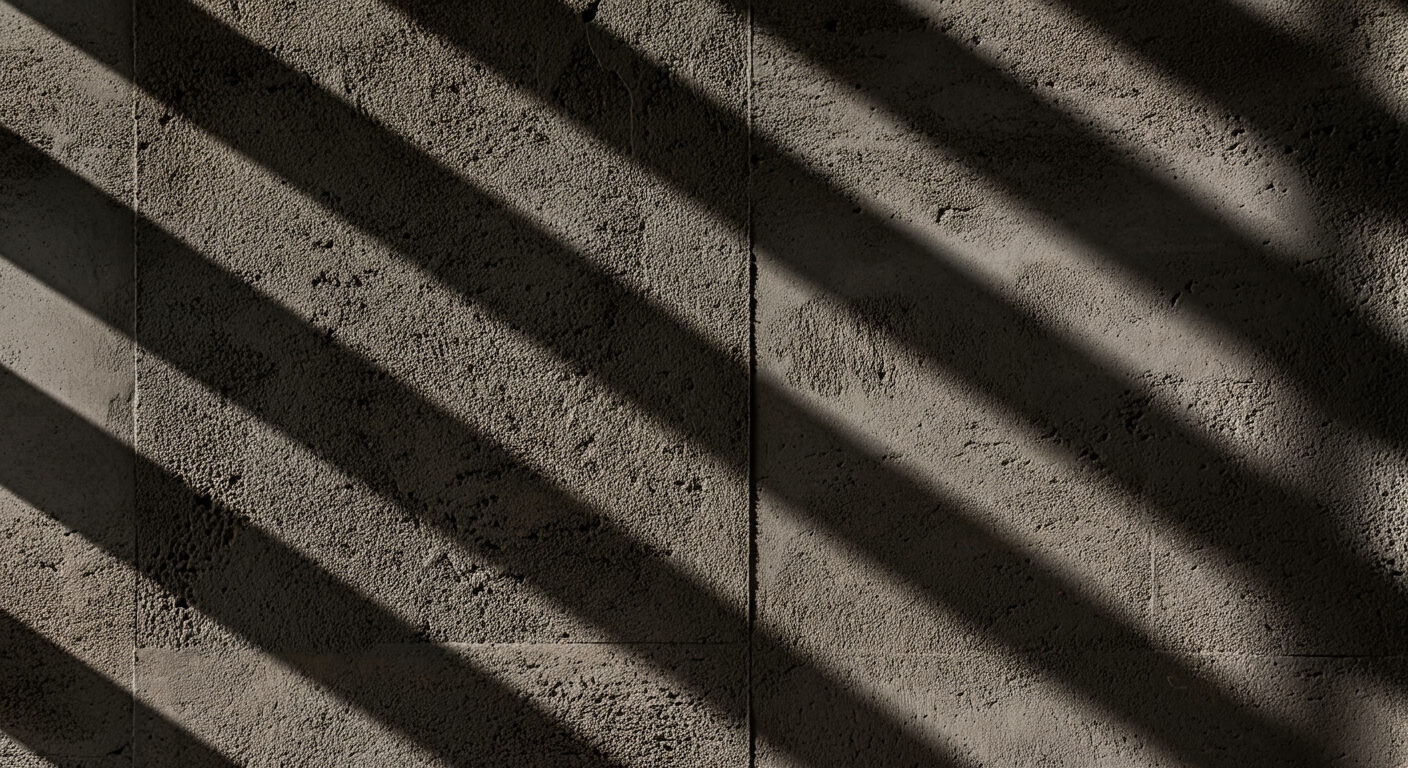
(fn) Functional Consulting Services
Operational Essentials: Structure, stability, consistency, and scalability. We handle the operational essentials you don’t have time for.
Constructability and Quality Control: Set the foundation for success.
See below for more details.
Operational Essentials
Build for tomorrow.
Assistance in the creation of items such as:
1. Standard Operating Procedures (SOPs)
Project Management SOPs – Define workflows for planning, execution, and closeout.
Safety & Compliance SOPs – Establish OSHA-compliant safety protocols.
Equipment & Maintenance SOPs – Outline procedures for inspections and servicing.
Quality Control SOPs – Ensure consistency in materials and workmanship.
Client & Contract Management SOPs – Standardize bidding, agreements, and dispute resolution.
2. Tracking Logs & Documentation
Project Progress Logs – Monitor milestones, delays, and completion rates.
Expense & Budget Tracking – Maintain financial oversight on materials and labor.
Equipment Usage Logs – Track machinery allocation and maintenance schedules.
Safety Incident Reports – Document workplace hazards and corrective actions.
Employee Work Hours & Productivity Logs – Ensure efficiency in labor management.
3. Defined Roles & Responsibilities
Executive Leadership – CEO, COO, CFO overseeing strategy, operations, and finance.
Project Management Team – PMs, site supervisors, and coordinators managing execution.
Estimating & Procurement – Cost estimators and purchasing managers optimizing budgets.
Field Operations – Foremen, tradespeople, and laborers executing construction tasks.
Administrative & HR – Office managers, payroll specialists, and HR handling compliance.
4. Organizational Charts
Company-Wide Org Chart – Visualize leadership, departments, and reporting structures.
Project-Specific Org Chart – Define roles for each construction project.
Subcontractor & Vendor Hierarchy – Clarify external partnerships and responsibilities.
5. Employee Evaluations & Templates
Performance Review Forms – Assess productivity, skills, and leadership.
Training & Development Plans – Track certifications and skill-building programs.
Job Description Templates – Standardize expectations for each role.
Onboarding & Exit Checklists – Ensure smooth transitions for new hires and departures.
6. Technology Integration
Cost code and tracking – Set up your back of house so the front of house can succeed.
Estimating – Assist with finding, selecting, and implementing a long term solution to estimating or improve the systems you have now.
Optimize – Identify pain points in the organization and see how technology such as AI or data integration can improve productivity.
Constructability | Quality Management
Plan smarter, build better, and deliver with confidence.
Constructability Essentials
Preconstruction Feasibility Analysis – Assess design efficiency, material availability, and site conditions before breaking ground.
Value Engineering Integration – Optimize designs for cost-effectiveness without compromising quality.
Material & Equipment Compatibility – Ensure selected materials and machinery align with project requirements.
Site Logistics Planning – Address access, staging areas, and workflow efficiency to minimize disruptions.
Design Coordination – Identify conflicts between architectural, structural, and MEP systems early.
Construction Method Optimization – Select the most effective techniques for speed, safety, and durability.
Risk Mitigation Strategies – Anticipate potential delays and develop contingency plans.
Stakeholder Collaboration – Improve communication between designers, engineers, and contractors for seamless execution.
Quality Control Essentials
Preconstruction and Coordination Meetings - ensure we are all prepared to meet expectations.
911 Problem Solving - Concrete specific reviews of on-site concerns as well as schedule reviews, oversight, recovery, RFI creation and submittals.
Material Verification Procedures – Ensure all materials meet specifications before use.
Benchmarking & Performance Metrics – Use KPIs to measure quality consistency.
Third-Party Engineering Services - Coordination with a third party if needed to create an engineered and stamped fix for on-site “opportunities”
Technology Integration for QC – Utilize digital tracking systems for real-time monitoring and/or tracking.
Continuous Improvement Programs – Establish feedback loops to refine processes.